Marked for Life: Inside the World of Safe Medical Device Laser Marking
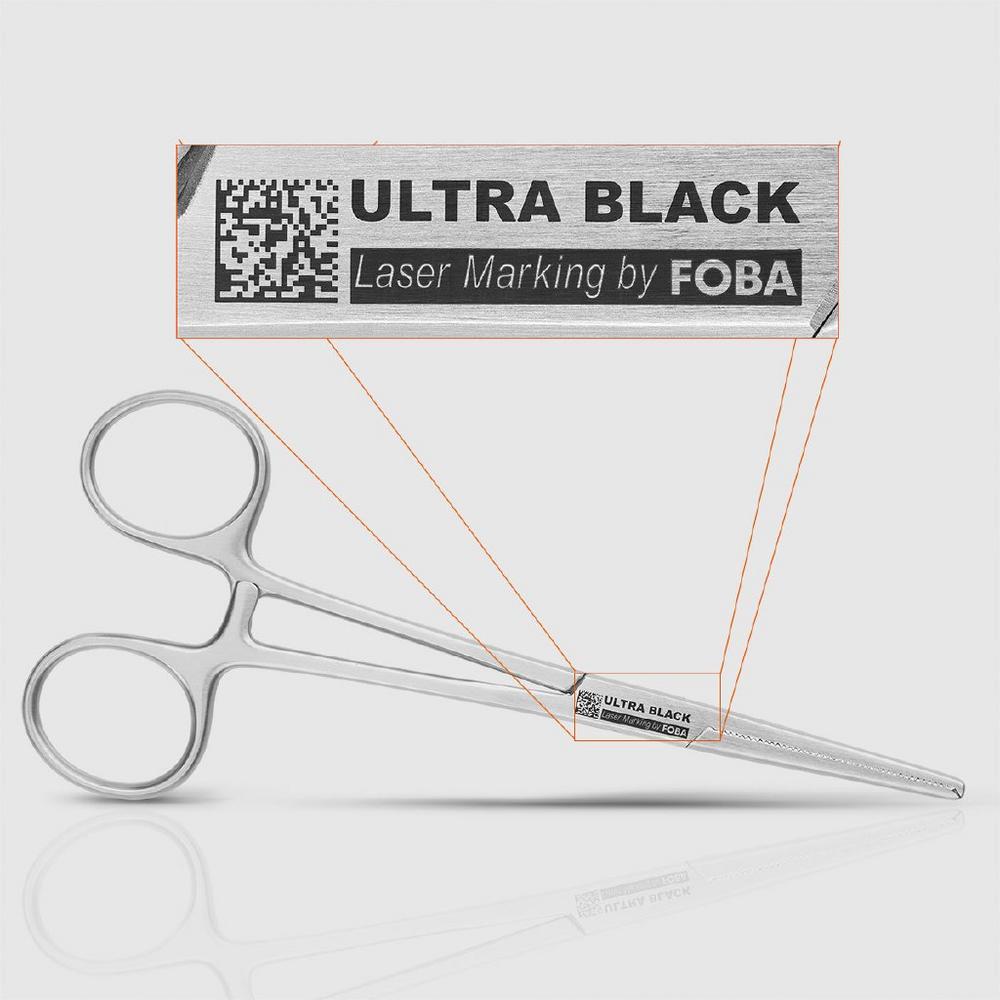
Breaking News:
Kathmandu Nepal
Donnerstag, Juli 17, 2025
But what exactly defines “safe marking”? How can maximum safety be built into the laser marking process from the very beginning? What needs to be considered when marking medical devices? And how can reliable, compliant markings be achieved?
Corrosion-Free Without Compromise: Can a Laser Marking Withstand 1,000 Reprocessing Cycles?
One of the key safety criteria for marking medical devices is corrosion resistance. This is especially relevant for metal-based products, such as stainless steel surgical instruments or titanium implants. If the products are intended for multiple uses, the marking must withstand repeated reprocessing cycles without causing corrosion or compromising legibility.
Medical technology service provider add’n solutions, based in Tuttlingen, Germany, and FOBA Laser Marking + Engraving, a manufacturer of laser marking systems for the medical industry, conducted long-term testing to evaluate the corrosion resistance and quality of laser markings. Laser-marked instruments were cleaned and passivated 1,000 times in a fully automated system, then autoclaved and exposed to periodic high-alkaline cleaning. The tests demonstrated that markings with FOBA’s ultrashort pulse laser F.0100-ir remained corrosion-resistant and reliably legible even after more than 1,000 cycles. “The marking is still perfectly readable. It outlasts the entire lifespan of the instrument. In fact, during testing, the material failed before the marking did,” explains Dominik Pfeiffer from add’n solutions.
For applications that demand maximum marking quality, legibility, and material integrity, Black Marking is the method of choice. This advanced technique uses ultrashort laser pulses to generate nanostructures on the material surface, resulting in a deep black, high-contrast mark with minimal thermal impact. Ultrashort pulse lasers like FOBA’s F.0100-ir are ideally suited for this process, offering precise parameter control and minimal thermal impact. Due to the highly focused and brief energy input, the resulting deep black marks form without significant heat exposure, preserving the material. The result: A marking that is durable, reliably legible from any angle, corrosion-free, biocompatible, biostable, and UDI-compliant.
Advanced laser technology provides all the prerequisites for safe and compliant medical device marking. With exceptional precision, maximum material integrity, and optimal legibility, it makes a decisive contribution to product safety and regulatory compliance.
Lasting Safety: Direct Marking of Sensitive Medical Devices
Thanks to continuous innovation, laser marking is increasingly being used for materials and products that previously required alternative methods – including sensitive plastics and critical devices such as pacemakers and active implants. Traditionally, ink-based methods like pad printing were used for these applications. However, in medical environments, inks and dyes are becoming less accepted due to issues related to biocompatibility and long-term readability. In addition, ink-based processes often result in high scrap rates due to smudging or fading, and require extensive quality control as well as drying times – all of which hinder efficient production.
In contrast, laser marking is a highly efficient, contact-free process. Without using potentially critical foreign substances, it enables durable, abrasion-resistant, and legible markings even on heat-sensitive materials. Alongside ultrashort pulse lasers, advanced UV lasers are ideal for marking delicate medical plastics. Because the marking is created through a photochemical effect and involves virtually no thermal stress, it is often referred to as “cold marking. The result is a smooth, hygienic surface with a pin-sharp, abrasion-resistant mark. “The latest innovations in UV laser technology allow us to mark materials that were previously considered unmarkable,” says Philipp Febel, Director of Product Management, Marketing & R&D at FOBA. “Our V-Series, with wavelengths of 355 nm (UV) and 532 nm (green), offers a wide range of applications and continues to impress both our customers and the laser experts in our application labs. This is especially valuable for medical device manufacturers who rely on direct laser marking to meet strict regulatory requirements. We can offer reliable, safe marking solutions even for the most challenging materials.”
From Installation to Quality Inspection: Process Reliability by Design
But even the best marking alone is not enough to ensure maximum safety in medical technology. The marking process itself and its qualification play an equally vital role in quality control. When laser manufacturers support qualification efforts, medical device companies benefit significantly. Understanding the optimal setup and adjustment of all parameters helps streamline the entire validation process. “Supporting IQ/OQ/PQ/MQ processes is a core part of our service offering,” explains Philipp Febel. “As laser experts, we contribute our knowledge directly to our customers’ workflows. This creates synergies that enable smooth, timely installation and qualification – the foundation for efficient, waste-free, and stable production.”
Documented quality and stable processes that ensure repeatable marking results are essential for validation, product safety, and UDI compliance. FOBA’s HELP (Holistic Enhanced Laser Process) is designed to meet these regulatory and production requirements. The laser-integrated IMP (Intelligent Mark Positioning) vision system detects the part’s position and geometry before marking and automatically aligns the laser accordingly – ensuring precise placement regardless of how the part is positioned in the marking field. This is especially important in the context of miniaturization in medical technology. Whether on dental implants, minimally invasive instruments, or catheters – automatic alignment and perfectly tuned parameters ensure reliable micro-markings where space is limited and precision is essential.
After marking, the result is verified inline – directly within the laser system – for both content and code quality. The results are documented automatically. This streamlined workflow reduces manual inspection, minimizes waste, and enables seamless documentation of marking quality. HELP delivers measurable value in medical device marking: more safety, more efficiency, less risk.
Smart, Scalable, Safe: Laser Marking in Medical Technology
Laser marking is more than just a marking method – it is the foundation of compliance, quality, and traceability in medical technology. Comprehensive consultation, application testing, and precise parameter adjustment are essential for meeting complex requirements. When expert knowledge, validated processes, vision-based precision, and documented quality come together, laser technology makes a decisive contribution to both product and patient safety. Beyond that, this efficient marking method meets all the demands of modern production environments: with extremely compact marking systems, intelligent interfaces, and digital, automated process solutions, the future is already built in.
More information:
FOBA Laser Marking + Engraving (brand of ALLTEC Angewandte Laserlicht Technologie GmbH) is one of the leading suppliers of advanced laser marking systems. FOBA develops and manufactures marking lasers for integration as well as laser marking workstations with vision assisted marking workflows. FOBA technology is being applied for the direct part marking of any kind of metals, plastics or other materials in industries like automotive, medical, electronics, plastics or tool, metal and mold making. With its worldwide sales and service branches and its headquarters near Lübeck/Hamburg (Germany) ALLTEC/FOBA is part of the Veralto Corporation.
FOBA Laser Marking + Engraving (ALLTEC Angewandte Laserlicht Technologie GmbH)
An der Trave 27-31
23923 Selmsdorf
Telefon: +49 (38823) 55-0
Telefax: +49 (38823) 55-222
https://www.fobalaser.com