Top 4 KPIs to monitor after a stocktake
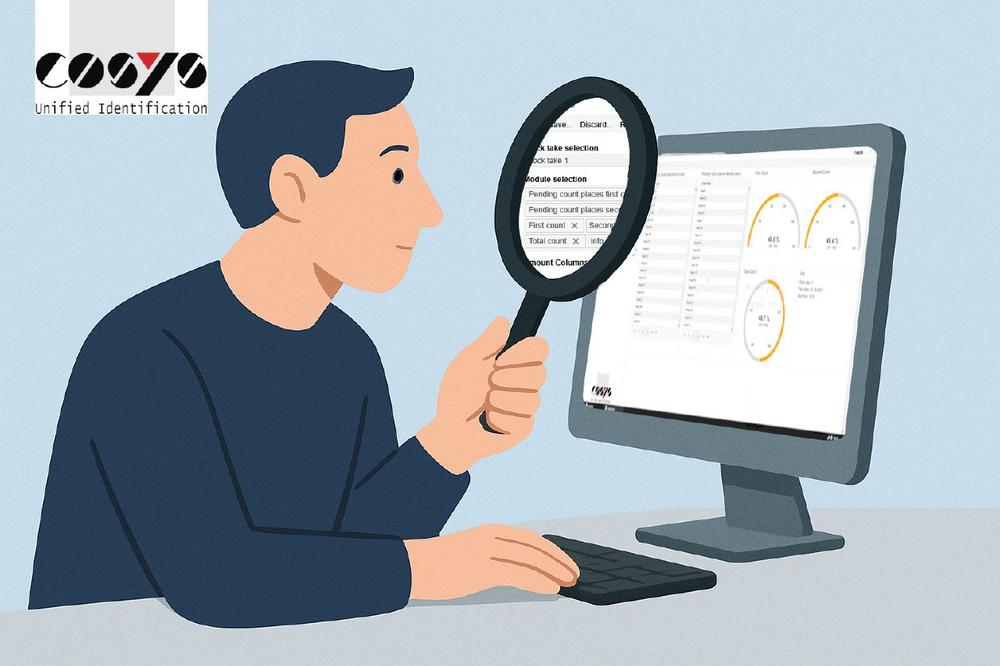
Breaking News:
Dymax präsentiert Prozesslösungen mit lichthärtenden Klebstoffen auf der European Battery Show 2025
Dymax to Showcase Light-Cure Solutions at The European Battery Show 2025
Mit Quellcode zum Quantensprung – wie Oliver Schulze den Mittelstand fit für KI macht
Streamline Your E-Commerce Fulfillment with COSYS 3PL Warehouse Software
Kathmandu Nepal
Donnerstag, Mai 22, 2025
KPIs provide measurable insights into how well your inventory processes are working—highlighting not just the accuracy of your stocktake, but also the efficiency of your team, the reliability of your systems, and the effectiveness of your overall inventory strategy. Without tracking the right KPIs, you risk repeating the same mistakes in the next cycle, or worse—making critical decisions based on flawed data.
In this article, we’ll break down the most important KPIs to monitor after a stocktake. You’ll learn what each metric tells you, how to calculate it, and how to use these insights to drive meaningful improvements. Whether you’re managing a single warehouse or multiple retail branches, these indicators will help you move from counting stock to managing it smarter.
Stock Variance (Quantity and Value)
One of the most revealing KPIs after a stocktake is stock variance, which measures the difference between the expected stock levels in your system and the actual physical count. This variance can be tracked both in terms of quantity (number of items) and value (financial impact). It’s a direct indicator of how accurately your inventory is managed—and where discrepancies may be costing your business.
Even small variances can signal larger issues. For example, consistent overages or shortages might point to mislabeling, incorrect receiving, poor picking practices, or even theft. Calculating the value of these discrepancies shows just how much they’re affecting your bottom line.
COSYS software makes variance analysis simple by automatically comparing physical and digital stock levels, generating variance reports, and highlighting problem areas—by item, location, or team. These insights allow you to dig deeper into root causes and take corrective action quickly.
Monitoring stock variance regularly not only improves inventory accuracy but also builds confidence in your data, enabling smarter decisions in purchasing, sales, and operations.
Duration per stocktake (or items counted per hour/days)
Efficiency matters just as much as accuracy in a stocktake—and that’s where the KPI Time per Count (or alternatively, Items Counted per Hour/days) becomes essential. This metric tracks how quickly your team is able to count inventory, providing insight into overall productivity and workflow optimization.
By measuring the average time it takes to count each item—or how many items are processed per hour—you can identify bottlenecks, highlight high-performing teams, and spot areas where additional training or better tools may be needed. Significant variations between locations or staff may point to inconsistent procedures or a lack of familiarity with equipment or software.
Total Value per Product Group
Tracking the total inventory value per product group after a stocktake provides valuable financial and operational insights. This KPI helps you understand how much capital is tied up in each category—such as electronics, apparel, consumables, or spare parts—and whether that distribution aligns with demand and sales performance. Disproportionate values in certain groups may indicate overstocking, slow-moving items, or poor forecasting. By analyzing product groups individually, you can make more informed decisions on purchasing, pricing, and space allocation. COSYS solutions support this analysis by categorizing items automatically and generating value-based summaries, enabling you to quickly spot imbalances and take strategic action.
Articles in Multiple Storage Locations
Monitoring articles stored in multiple locations is a crucial KPI for understanding inventory distribution and warehouse efficiency. When the same item is spread across several storage areas—intentionally or unintentionally—it can lead to confusion during picking, increased travel time, and higher error rates during stocktakes. It may also signal deeper issues, such as lack of space, poor slotting strategies, or inconsistent inventory practices. By identifying which articles are stored in multiple locations, businesses can consolidate stock, optimize layout planning, and reduce complexity. The stocktaking software makes it easy to detect these multi-location items through location-based tracking and reporting, helping ensure a more organized and transparent inventory structure.
Conclusion
Stocktaking is more than just counting—it’s an opportunity to gain valuable insights into your inventory processes. By monitoring the right KPIs after each stocktake, you can move beyond surface-level data and uncover the root causes of inefficiencies, inaccuracies, and hidden costs.
From identifying costly variances and measuring count efficiency to understanding product group value and managing inventory distribution, each KPI tells a part of the bigger story. Together, they give you a clearer picture of how your stock is performing—and where there’s room for improvement.
COSYS Ident GmbH, based in Grasdorf (near Hildesheim, Germany), has been in existence for almost 40 years and is one of the leading system houses in the field of mobile data capture solutions for Android and Windows. A medium-sized company that has been driving the development of identification systems since 1982 and today offers industry-specific complete solutions for almost all common business processes. From process design and concept development to hardware and software implementation, project management and customized maintenance contracts, we cover the entire range of system development, integration and support services. COSYS also offers a repair service, WLAN radio measurement and solutions for component traceability using DPM codes.
Cosys Ident GmbH
Am Kronsberg 1
31188 Holle – Grasdorf
Telefon: +49 (5062) 900-0
Telefax: +49 (5062) 900-30
http://www.cosys.de