Environmentally friendly accumulators: Efficient production processes for sustainable sodium ion batteries
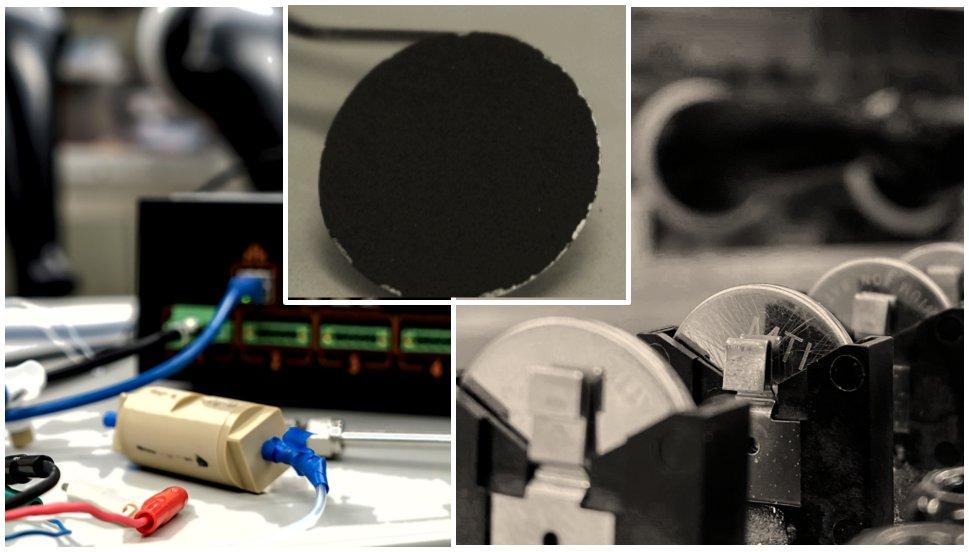
Kathmandu Nepal
Dienstag, Mai 7, 2024
Battery technology: sodium ions compared to lithium ions
Sodium ion batteries are seen as an attractive storage technology of the future. Sodium is available in abundance compared to the critical raw material lithium and can be extracted in a more environmentally friendly way. The actual environmental impact of sodium ion batteries lies in their manufacturing processes, for example through electricity and heating requirements. This is where the "NaNaBatt" project comes in and optimises the production processes of sodium ion cells in order to create a sustainable storage technology that is on a par with lithium ion cells in terms of performance. Although the relative energy density of sodium ion cells is lower than that of lithium ion cells, this can be compensated for by a cell volume that is around twenty per cent higher. In future, sodium ion cells will be suitable as stationary energy storage systems and for mobile applications. They have safety advantages over lithium-ion cells and are expected to have a longer service life in the future, which will significantly reduce their overall costs.
Process transfer: sustainable, innovative and cost-efficient
The aim of the "NaNaBatt" research project is to transfer established efficient processes in the production of lithium-ion cells – especially their electrodes – to sodium-ion technology at an early stage. This approach will enable environmentally friendly rechargeable batteries to reach market maturity more quickly. The used active materials are sufficiently available, easy to procure and easily recyclable. The result is to be demonstrated in the form of large-format cylindrical cells, which should have a so-called "state of health" of at least ninety per cent after a thousand charging and discharging cycles. The processing techniques developed for the innovative and environmentally friendly process strategy will then be analysed within an environmental performance evaluation.
The research project will run for three years and ends on 31 October 2026. The findings will ensure the long-term further development of German battery cell production. New expertise will strengthen Germany as an industrial location and the products developed will open up new markets. This will create skilled jobs and international competitiveness.
About IoLiTec
IoLiTec Ionic Liquids Technologies GmbH (IOL) was founded in 2003 and is a multi-award-winning innovative technology company that designs and manufactures highly specialised chemical products for various industries and for university research and development. The standard portfolio currently includes around 350 ionic liquids (IL) for laboratory scale and over 20 IL for pilot and industrial scale. IOLITEC also special-ises in R&D services and custom synthesis for IL technology.
The Battery LabFactory Braunschweig (BLB) is a research center of the TU Braun-schweig dedicated to the entire value chain of battery cell production. The BLB com-bines the competencies of 18 members in a transdisciplinary approach, three of whom collaborate in NaNaBatt:
About iPAT
The Institute for Particle Technology (iPAT) at the TU Braunschweig, led by Prof. Dr.-Ing. Arno Kwade, deals with process engineering questions related to electrochemical storage technologies, from basic research to process and production technology in industrial electrode manufacturing. The main focus of the work in the field of battery process engineering is the systematic investigation of the process steps of material synthesis, mixing and dispersing, coating, drying, compacting, and post-drying for the manufacturing of electrodes, recycling and safety investigations, as well as the simulation of each process.
About InES
The Schröder working group at the Institute of Energy and Systems Process Engineering at the Technical University of Braunschweig (InES) has many years of experience in the electrochemical analysis of cells and has carried out numerous preliminary studies in the field of optimising Na-based cells and the components used, which are currently being further expanded through operando measurements (gas analysis with GC-MS, confocal microscopy, ultrasound and acoustics). The Novák working group focuses on the electrochemical and operando/online analyses of battery cells and their components, with particular emphasis on clarifying the interactions between the individual components of the composite electrodes in order to better assess the safety and service life of the battery cells.
About IWF
The Chair of Sustainable Production & Life Cycle Engineering at the Institute of Machine Tools and Production Engineering (IWF) at TU Braunschweig, headed by Prof. Dr Christoph Herrmann, has extensive expertise in the ecological, economic and simulative-technological analysis and evaluation of industrial production and recycling process chains. The IWF is a founding member of the Battery Lab-Factory Braunschweig and coordinates the cross-sectional field of "Sustainable value chains and factory systems" with the topics of energy and material flow modelling, factory/process chain simulation as well as life cycle costing (LCC) and life cycle assessment (LCA). The IWF is also responsible for organising the annual International Battery Production Conference (IBPC) in Braunschweig.
Large-format round cells, LFP as a safe cell chemistry, energy-saving extrusion and an efficient contacting method are among the powerful ideas of a quarter of a century of EAS history. As a highly specialised niche supplier, EAS has been developing innovative cell and battery solutions at its Nordhausen production site for 25 years – including extremely robust and high-performance cells for applications in the aero-space, aviation, automotive, NRMM (Non-Road Mobile Machinery) and maritime industries. The EAS brand emerged from GAIA Akkumulatorenwerke GmbH, founded in Nordhausen in 1996. Since June 2017, EAS Batteries GmbH has been part of the Monbat Group.
EAS Batteries GmbH
Lokomotivenstraße 21
99734 Nordhausen
Telefon: +49 (3631) 46703-0
Telefax: +49 (3631) 46703-228
http://www.eas-batteries.com