Successful intralogistics of the future
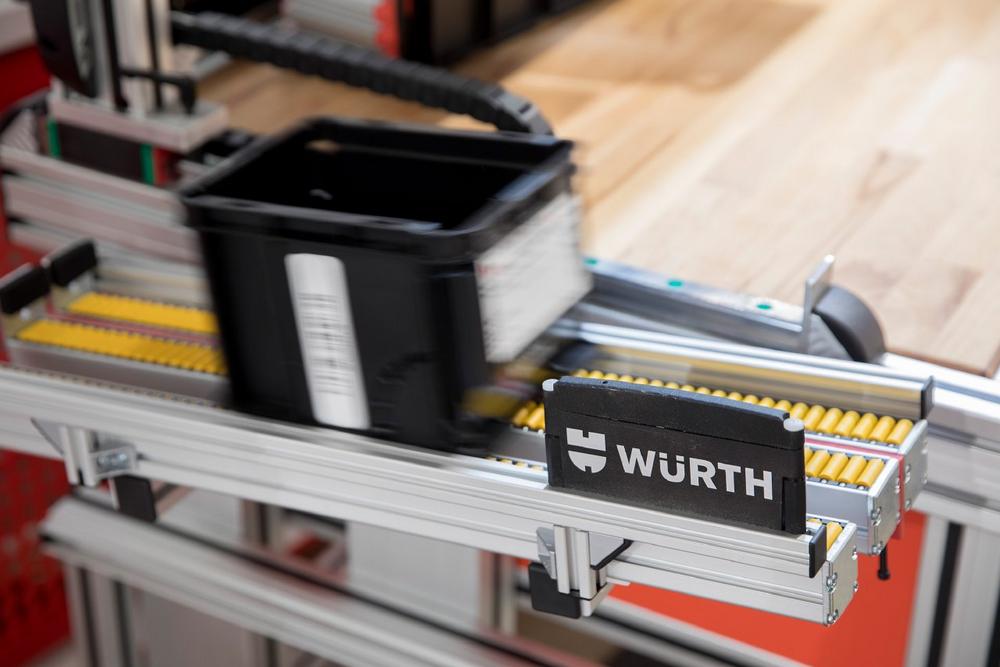
Breaking News:
Kathmandu Nepal
Montag, Mai 6, 2024
What does intralogistics of the future look like? Would it not be better to rely on fully automated systems, which apply lean management for inventories, automate re-orders and identify any fluctuations in demand at an early stage? This is achieved in a simple and secure manner with the supply of production resources using RFID Kanban. One of the top favourites for reordering C-Parts in a flexible manner is the battery-operated iPLACER®. The small handy module has an integrated reader and transmitter and can be placed anywhere – in the production, at workplace, in assembly, in logistics or intralogistics. At the workplace, the device independently triggers an order, as required. On the other hand, if it is attached to any flow rack, the user can map the incoming and outgoing goods, bookings, standing orders and order releases without manual efforts. RFID technology was implemented as order management system as well as inventory management system in iPLACER® for the first time. This has been a major step towards a connected, efficient value chain.
Since June 2022, iPLACER® has been ensuring increased productivity at Linde Hydraulics GmbH & Co. KG as well. Christoph Michalla, Head of Logistics at Linde Hydraulics explained its benefits and potentials and also shared the initial successes. “So far, a total of three iPLACER® devices have been installed successfully at our plant in Nilkheim, Germany. We use the module as an autonomous, independent ordering system – and it ensures complete transparency of our consumption and saves the time otherwise wasted in taking long trips to the centralised storage. The fact that the iPLACER® OP (Order Point) is portable and can be fitted at any desired place due to its compact size, is one of the biggest advantages for us. Not only on the load train, but also in the transit area from assembly to the supermarket, the device ensures maximum flexibility”, stated Michalla. Recording is also quite simple: Empty bins or Kanban cards with RFID tags are moved past the iPLACER® module and recorded on the order. An acoustic signal as well as a green LED light confirm that scanning was successful. The hydraulics manufacturer has benefitted from using the RFID Kanban in terms of saved time, thus ensuring that the employees are able to fully focus on their core competencies. “Our hydraulic requirements are streamlined and reordering is done in a fully automatic manner – and without doing anything manually”, said Michalla. The benefits are significant: Fully automated order triggering replaces cumbersome stocktaking and reordering at the customer’s location. By permanently covering the inventory, any fluctuations and peaks can be identified in time and thus the supply security can be maximised. In addition, the process can be economised significantly, as the high inventory levels can be reduced at the customer’s location and thus the space can be optimally utilised without any additional space requirements. Moreover, thanks to the automated reordering, production downtime is now a thing of the past. iPLACER® stands out as a system that can be used flexibly and placed anywhere, depending on the application. Absolutely versatile!
The basis for success: Tried and tested RFID technology
Under the brand “CPS® C-Product Service”, Würth Industrie Service offers manufacturing industry customers highly flexible Kanban solutions for efficient and transparent optimisation of existing production processes. Fully automated systems from the CPS®RFID family are well established for replenishment of production material. Radio Frequency Identification (RFID) enables radio-controlled data transmission directly from the customer’s production to the central warehouse of Würth Industrie Service. Through the automated and demand-oriented reordering of production materials, industrial companies benefit from maximum supply and delivery security. The basis for all this is always a Kanban bin and especially the patented Würth small load carrier, W-KLT®2.0, in the case of Würth Industrie Service. It is available in various sizes according to the VDA standard and is equipped with an RFID tag by default. Each transponder can be identified by a unique data security number. In the outgoing goods process, the ID of the bin is linked to the corresponding outgoing goods item. Using various RFID systems, the IDs of the bins can be read and transferred to the Kanban Management System of Würth Industrie Service for data transfer or automated reordering of C-Parts.
Read the success story on the website!
Within the Würth Group, Würth Industrie Service GmbH & Co. KG is responsible for supplying to the industrial sector. Since its foundation in the year 1999, the company is located at Industriepark, Würth in Bad Mergentheim, Germany with over 1,750 employees. As a one-stop C-Parts provider, the company offers its customers a specialised product range with over 1,400,000 items: from screws and tools to connection and fastening technology, technical chemicals as well as occupational safety solutions. Aside from the extensive standard product range, the strength of the company lies in its customer-specific, logistical and dispositive supply and service concepts as well as special parts. Under the service brand “CPS® – C-Product Service”, the company offers modular solutions customised as per the customer’s requirements. These consumption-based and demand-based systems streamline the processes for purchase, logistics and quality assurance while enabling the procurement of small parts in a cost-optimised manner. Logistic and dispositive services such as shelving systems that use scanners or a just-in-time supply using Kanban bin systems play a significant role in increasing productivity.
Würth Industrie Service GmbH & Co. KG
Drillberg
97980 Bad Mergentheim
Telefon: +49 (7931) 91-0
Telefax: +49 (7931) 91-4000
http://www.wuerth-industrie.com/pressebox