Perfect surface finishes for prosthetic and orthotic components from Ottobock
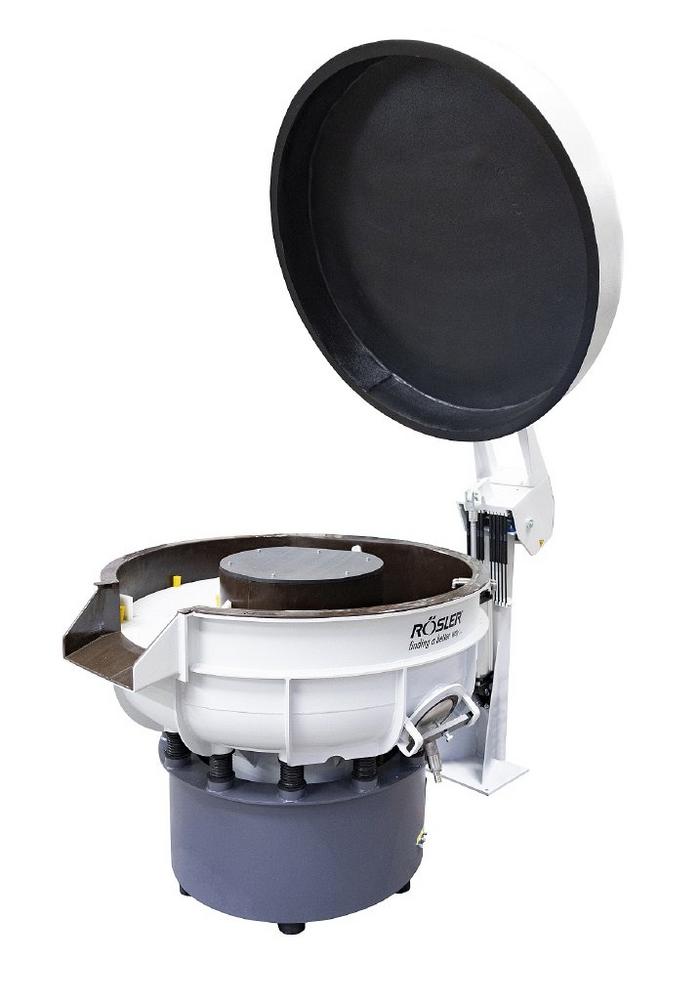
Breaking News:
Kathmandu Nepal
Samstag, Juli 5, 2025
For more than 100 years Ottobock’s innovative products and services in the fields of prosthetics, orthotics, human mobility and patient care have helped to achieve independence and quality of life for patients with restricted mobility. The company’s developments include the microprocessor-controlled knee join C-Leg, controlled by an app, the computer-controlled leg prothesis C-Brace, the multi-articulated hand bebionic and Juvo electrical wheel chairs. Since 2018 the Ottobock SE & Co. KGaA is also utilizing its mechanical / medical know-how for creating and maintaining a healthy working environment in a sustainable manner, for example, with the exoskeletal Paexo product range. A firm commitment towards creating more quality of life helped this company, founded in 1919, to become the global technological leader in “wearable human bionics”. With more than 8,000 employees and a sales volume of over one billion Euros, the company is represented in approximately 60 countries.
Newly organized manufacturing of components with optimized processes
For the production of its products the company is utilizing different manufacturing technologies. In this context mass finishing processes play an important role: On the one hand they must ensure that the products meet all functional requirements, for example, to be free of burs. On the other hand, the mass finishing operations must produce an optically pleasing surface finish. This also includes the creation of a highly homogeneous surface structure on the components, which are primarily made from aluminum and stainless steel. Some products even require a high-gloss polish. For many years, Ottobock has been using equipment and consumables supplied by Rösler.
When the company was looking for new mass finishing solutions for producing its components in an optimized and more sustainable manner, it was only natural that it turned to Rösler for help. For the initial processing trials the Customer Experience Center at Rösler represented the ideal platform. The center is not only equipped with the latest equipment for practically all finishing technologies. But it can also resort to a portfolio of more than 15,000 media and compounds, all developed and produced in-house.
Keramo-Finish operation replaces a process utilizing acidic compounds
Among other measures an acid-based process for creating a high-gloss polish was replaced by a tailormade Keramo-Finish operation. This includes the utilization of a porcelain polishing media in combination with a special paste and a brightening compound. The new, acid-free process allows the complete recycling of the process water. This has not only resulted in a significant decrease of the water and compound consumption but also in a sizable cost reduction.
The polishing operation takes place in a new, high-performance rotary vibrator, model R 780 EC. The special shape of the processing bowl creates a gentle, homogeneous flow of the media / work piece mix. This ensures that small and delicate as well as large and bulky work pieces are quickly polished and separated in an efficient and gentle manner.
The same operational benefits are also achieved with the second new rotary vibrator, model R 420 EC. Together with specially selected media and compounds Ottobock is using this machine for a broad spectrum of applications ranging from deburring and edge radiusing to surface smoothing.
For the eco-friendly cleaning and recycling of the process water the two mass finishing machines are connected to a semi-automatic Rösler centrifugal cleaning system, model Z 800.
Energy-efficient drying operation
For drying, the finished work pieces Ottobock chose the latest version of the RT 550 Euro-DH rotary dryer, also supplied by Rösler. This patented direct-heat dryer is equipped with an innovative heat-block heating system directly mounted to the base plate of the processing bowl. This ensures a highly efficient heat transfer with a minimum of heat loss. Thus, the dryer guarantees not only a quick, reliable and spot-free drying operation, but it also allows significant energy savings, which, compared to conventional drying systems, can amount up to 40 %. Therefore, the rotary dryer Euro-DH plays a key role in a more effective energy management within the framework of the recently introduced standard DIN EN ISO 50001. The new dryer also helps reducing the CO2 emissions and, as a result, represents an important contribution towards achieving the required environmental and climate targets.
For over 80 years the privately owned Rösler Oberflächentechnik GmbH has been actively engaged in the field of surface preparation and surface finishing. As global market leader, we offer a comprehensive portfolio of equipment, consumables and services around the mass finishing and shot blasting technologies for a wide spectrum of different industries. Our range of about 15,000 consumables, developed in Customer Experience Center and laboratories located all over the world, specifically serves our customers for resolving their individual finishing needs. Under the brand name AM Solutions, we offer numerous equipment solutions and services in the area of additive manufacturing/3D printing. Last but not least, as our central training center the Rösler Academy offers practical, hands-on seminars to subjects mass finishing and shot blasting, lean management and additive manufacturing. Besides the German manufacturing locations in Untermerzbach/Memmelsdorf and Bad Staffelstein/Hausen the Rösler group has a global network of 15 manufacturing/sales branches and 150 sales agents.
For more information please visit: www.rosler.com
Rösler Oberflächentechnik GmbH
Hausen 1
96231 Staffelstein
Telefon: +49 (9533) 924-0
Telefax: +49 (9533) 924-300
http://www.rosler.com