Vacuum in Woodworking – Part 1
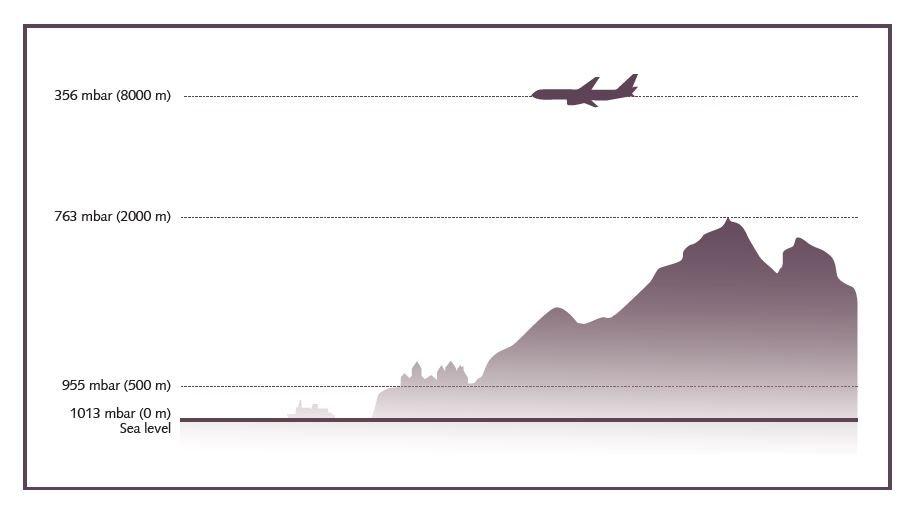
Breaking News:
Kathmandu Nepal
Samstag, Jun 1, 2024
Vacuum – what is it, really?
In woodworking, vacuum is mainly used for:
In wood processing, vacuum is used for:
Vacuum is most often used for vacuum clamping on CNC routers and other machining equipment. Here, the holding force of vacuum is used to quickly and securely fasten various panel materials or solid wood parts during woodworking, without leaving pressure marks. Handling equipment and assembly robots also often get their holding force from vacuum.
In purely physical terms vacuum – which is also known as underpressure – is a pressure range in which the pressure is lower than atmospheric pressure. The atmospheric pressure at sea level is 1,013 millibar (mbar), but constantly decreases in relation to altitude (Fig. 1). Weather conditions also influence the atmospheric pressure. In the context of vacuum technology, we simplify calculations by rounding the atmospheric or ambient pressure to 1,000 mbar. Pressures less than 1,000 mbar are referred to as vacuum or underpressure.
The most common unit of pressure for vacuum is millibar (mbar), although according to norms, this pressure range is supposed to be indicated in Pascal (Pa). In vacuum technology, we assume absolute pressures which theoretically start at 0 mbar and end at 1,000 mbar (= atmospheric pressure). The woodworking industry in particular still often uses bar, minus-bar (-bar) or the specification of pressure in percent (%) (Fig. 2).
Forces when clamping with vacuum
Will the clamped work piece hold? Is the vacuum sufficient or is the vacuum pump’s performance strong enough? These are questions that everyone has asked – at the latest when the spinning tool is approaching the clamped work piece.
From a purely theoretical perspective, the pressure between the work piece and the machining table, supporting surface or suction cup is reduced during clamping by extracting air and generating a vacuum. The atmospheric pressure is now higher and presses the work piece onto the machining table, thus ‚clamping‘ it.
Physical pressure is defined as a force that affects a specific area. Pressure is thus a function of force and area (Fig. 3).
In practice this means: the larger the supported work piece, the greater the holding force.
This can be best explained with an example:
A solid wood board is placed on the CNC router grid table for processing, and a seal is created with a rubber seal that fits the dimensions of the board (Fig. 4). A vacuum pump extracts the air between the wooden board and the grid table within the sealed area.
Calculation:
Atmospheric pressure: 1,000 mbar
Vacuum pump underpressure (working pressure): 200 mbar
Wooden board dimensions: 1,000 x 500 mm
Pressure differential:
1,000 mbar – 200 mbar = 800 mbar
= 80,000 Pa [N/m2]
Supporting surface = clamping surface
1,000 x 500 mm = 500,000 mm2
= 0.5 m2
Holding force
F = p x A
F = 80,000 N/m2 x 0.5 m2 = 40,000 N
= 4,000 kg
This means the solid wooden board with a surface of 0.5 m2 is held by the vacuum with a holding force of 40,000 N, which theoretically corresponds to the board pressing on the machining table with a weight of 4 tons.
If, under the same conditions, a solid 150 x 150 mm wooden board was clamped, the holding force would be F = 80,000 N/m2 x 0.0225 m2 = 1,800 N = 180 kg.
Now the question is how powerful the vertical holding force of the vacuum has to be to securely clamp a work piece. The example calculations show that the holding force for panel materials with large surfaces can be evaluated less critically than smaller wooden pieces or materials that are air-permeable or have uneven surfaces that lead to leaks.
In practice, the necessary holding force is difficult to determine because different factors like operational or clamping factors, cutting and feed speeds and directions, materials and frictional resistance have to be taken into account, so rules of thumb are normally used.
Various possibilities for vacuum clamping
An essential distinction is made between three possible vacuum clamping procedures:
Vacuum technology parameters
In principle, there are three parameters that need to be considered when selecting the most suitable vacuum technology.
Ultimate pressure
The ultimate pressure indicates the vacuum pump’s highest possible achievable vacuum level, or the lowest underpressure.
Pumping speed
This is understood to be the volume of air that a vacuum pump can extract within a certain period of time. The pumping speed is influenced by the geometry (volume) of the vacuum pump and its speed. The higher the pumping speed, the faster the air is extracted, and the ultimate pressure is achieved. High pumping speeds help compensate for leakage, for example, when using the nesting method.
Power consumption
Mechanical vacuum pumps are usually driven by an electric motor. Depending on the construction principle and efficiency factor, vacuum pumps consume different amounts of energy. To achieve the greatest possible energy efficiency, it is important to select a vacuum pump that produces the necessary performance with regard to ultimate pressure and pumping speed and simultaneously has the lowest possible energy requirement.
All three parameters are dependent on each other. Firstly, the pumping speed decreases as the vacuum pump gets closer to achieving the ultimate pressure (Fig. 4). Secondly, a vacuum pump’s energy requirement is lowest at a certain operating point.
Designing vacuum generation perfectly is difficult for laypeople, which is why we always recommend consulting a vacuum specialist.
In the second part of our "Vacuum in Woodworking" series, we will take a closer look at the different types of vacuum generation.
Busch Vacuum Solutions
Schauinslandstraße 1
79689 Maulburg
Telefon: +49 (7622) 681-0
Telefax: +49 (7622) 5484
http://www.buschvacuum.com