Molded elastic sensors: from scale-up to commercialization
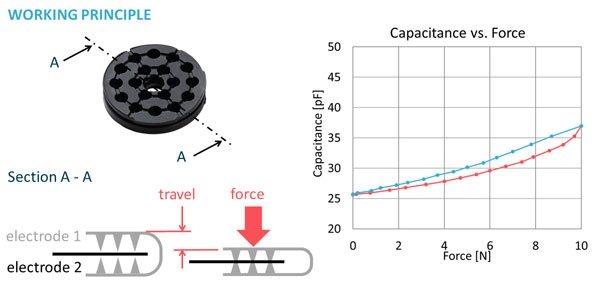
Breaking News:
Kathmandu Nepal
Mittwoch, Juli 2, 2025
The intelligent electronic skin
The human skin has an extraordinarily fine and complex sensor system for sensing touch and forces, which enables people to work intuitively and precisely. The material silicone comes very close to the mechanical properties of the skin. By properly designing the shape and conductivity of the material, silicone can be used as a mechanical transducer for forces and pressures. Such a silicone sensor consists of three elastic conductive layers stacked on top of each other. By this, the layers form a measuring capacitance which can be evaluated by electronic means. When pressure or force is applied to the silicone sensor, the conductive layers are moved in a defined manner towards each other, reducing the distance between the layers. This ultimately causes an increase in the electrical capacity of the silicone sensor, which can be measured by the electronics. By designing the measurement electronics as an AC voltage divider, it can precisely evaluate the sensor signal even with high-impedance elastomer material. Thanks to the good elastic properties of the silicone, a load can be repeated over a million times. Endurance tests with over 500,000 load cycles were carried out both at room temperature and at -40°C and +85°C, each also in combination with high relative humidity of up to 90%RH. In principle, silicone retains its elastic property over a very large temperature range of typically -40°C to +200°C and is therefore also suitable for use under demanding environmental conditions. Depending on the environmental conditions, aging is observed in the form of drift. This drift can be compensated by a reference sensor. By using several sensors at the same time, a spatial resolution can be realized, e.g. to determine the direction of the force.
Proven manufacturing processes
Electrically conductive solid silicone with a hardness of 60 Shore A is used as the base material for the silicone sensor. The conductivity is achieved by adding carbon-based particles. In the crosslinked state, the solid silicone mixture has a conductivity of more than 0.10 S/cm and is commercially available in large quantities. The sensor is shaped using a compression tool under high pressure and temperature. The compression process enables the processing of highly filled, very viscous silicone material and three-dimensional shaping in one step. The spring elements for supporting the individual sensor layers and the general shape of the finished sensor are simultaneously produced in the molding process. After removing the cross-linked silicone part from the mold, the component is folded into the three-layer configuration. The spacers between the layers are designed like small membranes, which serve as restoring elements. They hold the layers in position and act as elastic springs generating the force-dependent capacitive sensor signal. The electrical connection of the sensor can be made via a connector, which is connected to the conductive silicone by crimping. Unlike printing, compression molding enables the production of real three-dimensional free-form surfaces. This results in new freedoms in the design of products to adapt e.g. to ergonomic use. Most experience is currently available with sensors in the dimension range from 10 to 20 mm in length, which can determine forces of several 10 N with an accuracy well below 1 N.
Application examples
The silicone sensor is characterized by high elastic deformability in the direction of force or pressure. This means that it can be easily integrated into soft materials such as textiles and foams. Due to its elasticity, it can ensure a mechanical preload of the system. This simplifies assembly, especially in curved and complex structures. The silicone sensor is therefore suitable, for example, for use in automated processes. The low weight is particularly important for mobile robots and portable exoskeletons. Force sensors on grippers can support the automatic detection of objects. Studies have shown that robots which shall recognize objects that are unknown to them need "tactile" characteristics such as the rigidity of the objects in addition to image recognition. Force sensors in the feet of robots and exoskeletons help maintain balance. In medical technology, the sensor is of interest for controlling prostheses and measuring pressure points on the soles of the feet and pressure bandages. In automotive engineering, there are already feasibility projects for controls in the steering wheel. By incorporating several sensors in the central area of the steering wheel, force-controlled horn functions and gesture control can be implemented with the same components. Due to its high flexibility in all directions, the sensor can efficiently compensate for tolerances in assembly and leather covering and ensure good mechanical coupling to the user interface.
Summary
The Sateco Group has advanced the industrialization of silicone force sensor and is working with several manufacturers of industrial goods and automobiles to integrate it into mechanical systems. Samples of a standard version are available for this purpose, including evaluation electronics and software for visualizing the measurement data. There is also in-depth knowledge and experience in the use of silicone for sensors based on resistive and inductive measurement principles. This enables the development of customer-specific solutions, taking into account the material properties and electronic interface beyond the capacitive silicon sensor.
The Sateco Group is one of the world’s leading manufacturers of keypads and silicone sensors. Sateco combines years of know-how and innovative technology with customized solutions, and it sets standards for creating controls and switches. This family-owned company with approx. 800 employees is headquartered in Schwerzenbach, Switzerland and maintains subsidiaries in Europe, the U.S., and Asia. With consistent quality management and immense innovative strength, Sateco creates tangible added value for its prominent customers from many different industries. For more information, please visit satecogroup.com.
Sateco
Sonnenbergstrasse 72
CH8603 Schwerzenbach
Telefon: +41 (44) 90562-62
http://satecogroup.com