„Modern Packaging Minimises Waste of Resources“
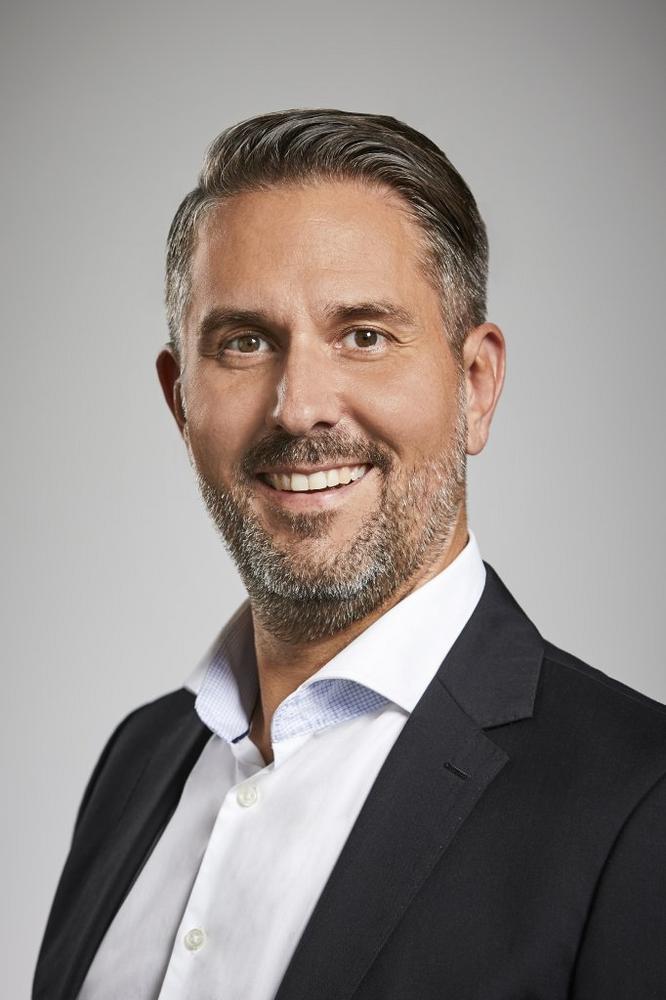
Breaking News:
Kathmandu Nepal
Dienstag, Mai 28, 2024
The Managing Director of Hugo Beck Maschinenbau GmbH & Co. KG in Dettingen/ Erms, Timo Kollmann, reports in an interview on concrete steps the company has taken towards the circular economy.
Do you use recycling and waste avoidance concepts in your own production?
In addition to the now obligatory sorted disposal of production waste and operating materials, we generate electricity for our production, assembly, and administration building with our own photovoltaic system. We also feed some of it into the power grid. We have also invested in charging points for electric vehicles and have a very well-received leasing offer for e-bikes. A good third of our employees now come to work by bike. The electric support is welcome to them in our mountainous region. In our production and assembly, we rely on state-of-the-art energy-efficient machinery from machining to painting. Especially in the paint shop, it’s not just about saving energy, but we also have cleaning systems with solvent recovery there to make the processes as environmentally friendly as possible.
What Circular Economy solutions do you offer your customers?
This starts with the drives of the packaging machines we build. Here we consistently use servo motors that recover energy during braking and feed it back into the system. With modern drive technology, however, we are above all able to optimise the packaging processes themselves. In this way, our customers save on consumables on a grand scale. This applies to both their films and paper packaging. A good example is the cucumber. After discounters stopped shrink-wrapping them in film, they had to dispose of up to 40 per cent due to transport damage and premature spoilage. We have developed solutions to work with much thinner films. Instead of 40 to 60 micrometres (µm), they are now less than 10 µm thin and made of recyclable mono-material. With the same amount of plastic, four to six times more cucumbers are packed and the unnecessary waste of energy and resources due to the losses is put to an end. Our machines can not only process thinner material, but also make better use of the films through optimised cutting. And on top of that, our customers can use films with a high recyclate content. Among other things, we have very good experience with films made of up to 80 per cent recyclate. The technical design plays a decisive role here: if you invest in cheap drive technology and immature web guiding, you end up paying for it through the additional consumption of film, paper, and energy – and thus pollute the environment. The extra cost of modern technology is usually amortised within the first two years.
How does the topic affect your research and development and your cooperations with customers and material suppliers?
We are working more closely together and jointly scrutinising which material meets the requirements for the respective application with the lowest energy and ecological footprint. Currently, many customers rely on paper. We are working on expanding its range of applications. For example, in a funded research project with a university, we are developing bio-based coatings from waste from wine production, which make paper water-repellent but still recyclable. Our part is to develop the processing methods for these papers. But there are regulatory limits to their use. Frozen pizza, for example, may not simply be packed in a carton: The obligatory film prevents contamination by outgassing chemicals. Food and drug safety remain the benchmark when we develop new approaches. In other areas, I too consider some packaging to be dispensable. In close cooperation between material development, mechanical engineering, and users, we should use all possibilities to minimise the ecological footprint of packaging. The key to this is reduced material use and recycling-friendly monomaterials. At the same time, it is important to establish functioning disposal and recycling systems all over the world.
Is the demand for your Circular Competence increasing worldwide – or is this more of a regional phenomenon?
Fortunately, this is now a global trend. Whereby the orientation also depends on regional conditions. Where no trees grow, our customers tend to use plastics rather than paper. In densely wooded regions it is the other way round. But in general, environmental awareness is on the rise and is increasingly influencing which machines our customers invest in.
Environmental protection is often driven by regulation. Are the framework conditions right for entering the Circular Economy?
Even before the plastics debate, we worked hard to make packaging as environmentally friendly as possible. Because they are often indispensable. Worldwide, about one third of all food is lost every year along its value chain, i.e., from harvest to consumer. Not only food is lost, but also the resources used for cultivation, harvesting, processing, transport, and storage. One key to minimising this waste of resources is packaging. In pharmaceutical, medical, and other sectors with high hygiene requirements, products will remain packaged. It is therefore important to search with a cool head on a scientific basis for those solutions with which the respective packaging requirements can be implemented with the smallest ecological footprint. It is not the case that paper is always the more ecological solution than plastic. The weighting is shifting towards plastics as the proportion of recycled materials increases. This is because a certain amount of fresh long fibres will always be necessary in packaging paper and cardboard. Hugo Beck is successful with both film and paper packaging technology. So, I am not biased, but simply wish for regulatory decisions that are preceded by well-considered and technically sound decision-making processes. Only in this way will we succeed in effectively reducing the burden on the environment. We no longer have time for pure symbolic politics.
The VDMA Printing and Paper Technology Association is the mouthpiece of around 170 manufacturers of equipment and systems for the printing and print processing, paper manufacturing and converting, and auxiliary materials and equipment sectors from Europe. It thus represents around 90 per cent of the industry. The trade association offers its members services, for example on topics such as trade fairs, public relations, technology and research.
VDMA, Verband Deutscher Maschinen- und Anlagenbau e.V.
Lyoner Str. 18
60528 Frankfurt
Telefon: +49 (69) 6603-0
Telefax: +49 (69) 6603-1511
http://www.vdma.org/