Reducing textile microplastics – The entire life cycle of clothing should be taken into account
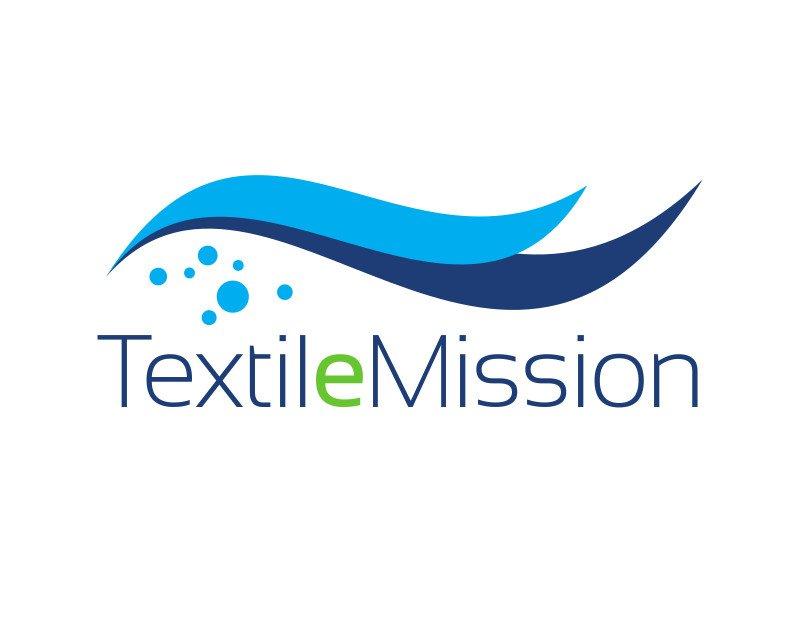
Breaking News:
Kathmandu Nepal
Freitag, Mai 3, 2024
Be it in water, air or soil – microplastics are now found everywhere in the environment. Along with car tires, construction coatings, sports fields and playgrounds, and plastic waste in the environment, textiles made from synthetic materials such as polyester are also a relevant source. "Fiber fragments, for example, can cause inflammations and entanglements in the digestive tract of marine organisms. Also, growth and reproductive limitations as well as behavioral changes have already been observed," points out Caroline Kraas, project manager for microplastics at WWF Germany. "From a sustainability perspective, it was essential to span the scope of TextileMission’s research as far as possible. The issue is not only the particle discharge caused by the household washing of synthetic textiles. Considerable emissions already occur in textile production, abrasion occurs during wear, and fibers are released from landfills. We knew: prevention must start as early as possible and throughout the life cycle."
Washing and drying tests reveal extent and causes of textile microplastics
In order to be able to develop the best possible prevention strategies, the TextileMission partners first addressed questions on how and where textile microplastics are formed and what influence washing behaviour has. Answers were sought and found by means of extensive washing and drying tests with commercially available sports and outdoor textiles. One test result stands out: by far the most fibrous microplastics are released during the first three washing cycles of a new garment. "This indicates that the product often still contains fibrous microplastics from production, transport and trade, which are only discharged during household washing," explains Prof. Dr. Maike Rabe, head of the Research Institute for Textiles and Clothing at Hochschule Niederrhein. One approach to solving the problem, which all TextileMission partners believe is necessary, is an optimized and clean production process. In addition, before garments enter the market, efforts should be made to ensure a controlled cleaning of the products, including the safe disposal of the fibrous microplastics.
Consumers are also wondering what contribution they can make. "It is recommended to always load the washing machine as full as possible. When the load is low, textiles are exposed to higher mechanical stress and therefore release more fibrous microplastics. Shorter washing times also have a positive effect," adds Maike Rabe. In general, it is advisable to avoid "fast fashion" when it comes to buying clothing, but to opt for higher-quality products and to wear them for as long as possible.
Wastewater treatment plants have good retention of textile microplastics
What happens to textile microplastics once they enter wastewater via the washing machine? The team of the Institute of Water Chemistry at the Technical University of Dresden investigated this question using, among other things, a laboratory wastewater treatment plant that simulates different mechanical, chemical and biological treatment stages. "Our experiments indicate that up to 97 percent of textile microplastics could be retained by wastewater treatment plants," says the head of the institute, Prof. Dr. Stefan Stolte. "Technically, it is even possible to treat wastewater so that it is free of microplastics. However, this goes along with a lot of effort and costs," Stolte continues. Therefore, instead of maximizing efforts to get microplastics out of the water cycle, it would be better to work on avoiding the emission in the first place.
Product development: machine parameters and alternative joining techniques as levers
Development of sports and outdoor textiles made of polyester, which are already designed and manufactured to reduce microplastic emissions, was one of the subjects of research at Hochschule Niederrhein. Prof. Dipl.-Des. Ellen Bendt, Lecturer at the Department of Textile and Clothing Technology, explains two approaches at different stages of the production chain. "Already in the manufacturing stage of the textile fabric, fibrous microplastics are produced due to the mechanical stress on the yarns in the knitting process. Experiments with our institute-owned large circular knitting machine show that changing a few machine parameters leads to a reduction in particle emissions." However, changes in machine parameters also alter other fabric properties such as performance values, which is why further research is needed in this area. When the fabric is later processed into garments, there are also promising levers. "Conventional cutting and joining processes increase the emission potential. Alternative processes such as the cutting with the laser cutter and any edge finishing with a high coverage of the cut edges show the best effect and could lead to reducing the discharge of fibrous microplastics," says Ellen Bendt.
Alternative fiber materials in the sustainability check
"For us as a manufacturer of outdoor clothing, textile technology approaches are an important lever for reducing microplastic emissions and at the same time meeting the expectations of our target group in terms of quality and functionality of our products," states Robert Klauer, project manager textile innovation – microplastics, VAUDE Sport GmbH & Co. KG. "In addition, our goal is to apply alternatives to virgin polyester in as many products as possible in the future." This was one of the reasons why, as part of TextileMission, the project partners looked at the potential, but also the ecological and social sustainability risks, of fibers made from recycled and biodegradable materials. "Both recycled polyester and fibers made from cellulose have the potential to be a more sustainable alternative in terms of feedstock acquisition, production and disposal," summarizes Caroline Kraas from WWF Germany. "However, textile manufacturers should keep various social and environmental sustainability factors in mind when sourcing." Among other things, the region of cultivation, the cultivation methods, the technologies and energy sources used, transport, production and processing procedures, the use phase and end-of-life handling and, last but not least, social and labor standards play a role in this regard.
Biodegradability of fiber materials in wastewater treatment plants: viscose performs well
The extent to which materials declared as biodegradable actually degrade in a wastewater treatment plant was another research focus of TU Dresden within the framework of TextileMission. Prof. Dr. Stefan Stolte explains the corresponding results: "As expected, within the test period of 58 days, pure polyester was almost not degraded at all, but cellulose fibers such as viscose were almost completely degraded." However, Stefan Stolte warned against a prematurely optimistic generalization of the results: "These statements on biodegradability refer to the sewage treatment plant system – the degradation behavior in the deep sea, for example, runs under completely different conditions." In addition, he said, it has been shown that dyes and other additives used in the chemical finishing of textiles can negatively influence degradation behavior.
Outlook: Only a mix of solutions will lead to fewer textile microplastics
From innovative processes in production to the use of alternative materials – after three and a half years of research, various promising approaches to reducing textile microplastic emissions have emerged, but there is also a need for further research and development. It became clear that only an interdisciplinary approach will be successful, which a) takes into account different stages of the production chain and the life cycle of textiles and b) works across industry and research disciplines. "The sporting goods industry is taking on the continuing challenges of reducing textile microplastics," says Alexander Kolberg, policy officer at the Association of the German Sporting Goods Industry. "As an industry association, we will continue to participate in relevant initiatives and research projects to help develop sustainable solutions for the environment, consumers and our industry."
Further information on TextileMission (in German):
The 46-page final publication of TextileMission with further results: https://textilemission.bsi-sport.de/fileadmin/assets/Abschlusspublikation/TextileMission_Abschlussdokument_Textiles_Mikroplastik_reduzieren_9.06.2021.pdf
TextileMission – the video: https://textilemission.bsi-sport.de/aktuelles/textilemission-der-film-feiert-premiere/
Images and contact persons will be provided upon request.
Background:
TextileMission was a multidisciplinary project that aimed at reducing the environmental impact of fibrous microplastics released by textiles made from synthetic fibers such as polyester. TextileMission ran over a period of three and a half years and was funded by the German Federal Ministry of Education and Research (BMBF) as part of the funding priority "Plastics in the environment – sources, sinks, solutions" with around 1.7 million euros. As project partners, the following nine organizations from research, the sporting goods industry, the household appliance and detergent industries and environmental protection contributed their respective expertise to the project: As consortium partners: Bundesverband der Deutschen Sportartikel-Industrie e.V., Hochschule Niederrhein – Research Institute for Textiles and Clothing, TU Dresden – Institute for Water Chemistry, VAUDE Sport GmbH & Co. KG and WWF Germany. As associated partners: adidas AG, Henkel AG & Co. KG aA, Miele & Cie. KG and Polartec LLC. Further information can be found here: http://textilemission.bsi-sport.de/
Bundesverband der Deutschen Sportartikel-Industrie e.V. (BSI)
Mühlenweg 12
53581 Bad Honnef
Telefon: +49 (2224) 76381
Telefax: +49 (2224) 75940
http://www.bsi-sport.de