Quality and energy efficiency in veneer drying
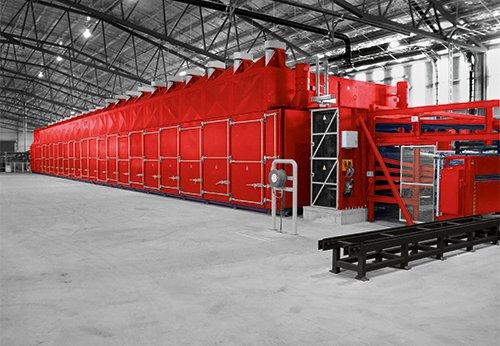
Breaking News:
Kathmandu Nepal
Freitag, Mai 3, 2024
The entire wood processing world meets in Hanover/Germany from 27 to 31 May – at LIGNA. Under its motto "Grenzebach, we do drying better" Grenzebach (Hall 26, Stand F57) presents in a world premiere a moisture and thickness detection system for veneers that gives a great boost to quality and energy management in wood processing companies. The system can measure the moisture content and thickness of wood veneers separately or at the same time. "The new system is preferably used upstream and downstream from the dryer to allow optimum control of the energy input. It is possible to both show trends over a time period and create a mapping across different veneer species," says Dr Christoph Habighorst, Vice President Sales Building Materials Technology at Grenzebach BSH.
Moisture levels of more than 100 per cent abs. dry
The non-contact measuring system can also be used directly after veneer peeling because even very high moisture levels of more than 100 per cent abs. dry are handled with great accuracy. "Our system is ideal for the "green" peeling line end of the production line. In addition to the moisture content of a veneer sheet, its thickness can be continuously determined as well. This supports the control of the peeling line, giving the Grenzebach system a clear edge over our competitors," explains Dr Habighorst. A special technique optimises the stability of the readings, taking into account varying gaps between the sheets and the waviness of the veneers. The innovative system comes with all functions implemented for the major hardwood and softwood species used in industry.
Grenzebach: partner for product innovation
"Grenzebach – we do drying better": Its extensive and profound expertise in veneer drying has made Grenzebach a genuine partner of the wood processing industry, and through intense cooperation with companies from that sector new building products could be developed and made ready for the market. This was possible thanks to significant progress in the corresponding production and processing technologies. "Working intensely to find solutions to specific questions has helped us to gain market leadership in these fields very quickly," underlines Dr Habighorst. At LIGNA Grenzebach presents a number of innovative building products and materials that Grenzebach drying and handling technology has made possible. "Our technology also benefits from decades of experience with numerous plants and systems. With over 400 of its dryers installed worldwide, Grenzebach is among the world’s leading suppliers of plants and components for the production of wood veneer. Another 400 plants installed in other building materials sectors underline the diversity of the Grenzebach production know-how." In addition to peeled veneers, Grenzebach systems also process decorative veneers, which are used in the furniture industry and can be found on yachts, in hotels and other interior-design applications.
High output, reduced energy consumption
The special features of its drying technology are of course what Grenzebach’s presence at LIGNA focuses on: The latest peeled-veneer dryer, for instance, can be fed at a speed of up to 23 cycles/minute. Veneers can be overlapped at the dryer infeed. This serves to optimise the utilization of the dryer decks and to make drying more uniform – with the shrinkage of the sheets during drying already allowed for. The Grenzebach specialists have improved the air flows yet again: Flow-optimized air distribution zones and a balanced air volume over all decks provide optimum, uniform drying results. "A higher dryer output at a reduced energy consumption, resulting in a high-quality finished product: Our technology is designed to take all customer target parameters related to the production process into account," says Dr Christoph Habighorst. Optimised nozzle boxes with saw tooth tread design provide for a homogenous distribution of the drying air over the entire dryer width. This also
minimises the risk of veneer jams in the dryer, which are a well-known issue.
Modular design for all requirements
"Grenzebach – we do drying better": The Grenzebach veneer dryer has a modular design and can thus be optimally set up on site in line with the prevailing conditions and requirements. The 2.25 m long modules are combined to obtain the required dryer length. Dryers are available with four, six or eight decks – and working widths of 4 metres, 4.80 metres, 5 metres, 5.8 metres, 6.2 metres. Access to the dryer inside is through doors clad with aluminised sheets. Each door extends over an entire section and, thanks to its special design, can be opened with one hand. Curved elements instead of rectangular ones with corners hold the specially developed door seals and ensure durable and perfect sealing. Whatever the size and design details of the dryer may be, no special foundation is necessary, and all Grenzebach dryers come with an insulated dryer floor – highest energy efficiency always being a top priority.
Grenzebach belt dryers are equipped with a special sine wave guide system
between the carry and cover belts. It exerts a certain pressure and thus helps to reduce the waviness in particularly wet and difficult to dry veneer species such as beech or poplar. Seal sections at the inlet and outlet prevent water condensation and pitch build-up on the dryer walls. Very high humidity levels (up to 900 g H2O/kg air) in the different dryer sections would not be possible without the extremely tight structure of the Grenzebach dryer.
Planning and optimising using virtual reality
What can and should the dryer system look like in detail to meet our requirements? And where in the process chain can things be further optimised? To help answer these questions for companies in the wood processing industry the Grenzebach experts increasingly use virtual reality (VR). "To show what digitisation has already made possible in daily operations today and what potential there is for the future: Presenting this at LIGNA – and discussing these topics and exchanging views about them is something that greatly matters to us," emphasises Dr Christoph Habighorst. There is a broad spectrum, extending from VR-assisted planning and design of production lines up to simulating complex process chains. And of course visitors to Grenzebach’s stand at LIGNA can make a tour of a veneer mill with virtual reality glasses straight away.
Upgrades instead of downtimes
At LIGNA Grenzebach also raises awareness of how control system upgrades can prevent plant stoppages and downtimes. Habighorst: "Providing services that have a tangible added value for the customer is our top priority – and that definitely includes revamping installations with the latest technology for control and operation. What the benefits of a VNC upgrade look like is something we demonstrate at our stand using practical applications.“
Strategic partnership with HOMAG Group
Visitors can carry on the momentum gathered at the Grenzebach stand and move on to Hall 14, Stand H34: That is where the HOMAG Group, a strategic partner to Grenzebach, presents new developments in integrated solutions for production processes in the wood processing industry and the crafts. Grenzebach’s input here are automated guided vehicles for optimised materials, production and goods flows.
More than 400 plants for the veneer industry supplied by Grenzebach are in use worldwide. The sorting and grading systems reach stacking speeds of up to 300 m per minute. Another advantage is uniform drying over the entire width and all dryer decks. Dryers with eight decks and up to 6.2 m working width are in use.
Grenzebach Group
Albanusstrasse 1
86663 Asbach-Bäumenheim
Telefon: +49 (906) 982-2000
Telefax: +49 (906) 982-108
http://www.grenzebach.com/de/